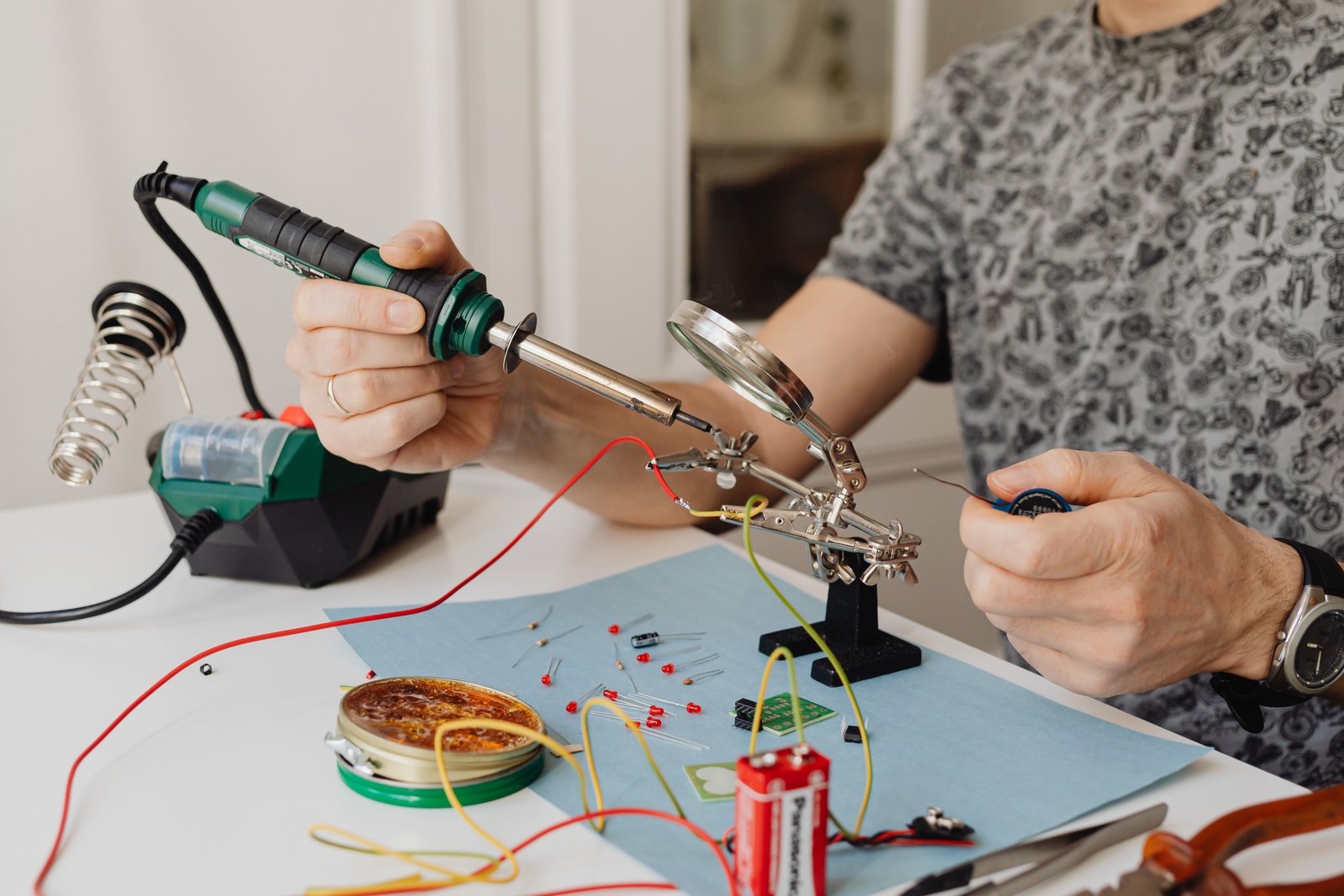
Quality Info
At Rasph Corp, we understand the importance of providing our customers with high-quality products and services. Quality is an integral part of our production process and we make sure to implement it at every step. From Design and Engineering to manufacturing and testing, our team members are responsible for ensuring that our products and services meet or exceed customer expectations and industry standards.
Why Choose Us
All Team members are trained to IPC/WHMA-A-620 Workmanship Standards
At Rasph Corp, we believe that providing our team members with the proper training and tools is essential to producing high-quality products. That's why we have made it a priority to ensure that all of our team members are trained to IPC/WHMA-A-620 Workmanship Standards for Cable and Harness Assembly. This training program covers all aspects of cable and harness assembly, including proper soldering techniques, wire preparation, and inspection procedures.
By providing our team members with this training, we are able to ensure that all of our products meet the highest industry standards for quality and workmanship. This, in turn, enables us to provide our customers with products that are reliable, consistent, and perform to the highest levels.
Quality is our top priority and even though we are a small team, we make sure to implement the best practices to deliver products that meet or exceed customer expectations.
Welcome to Audit Our Facilities
At Rasph Corp, we understand the importance of transparency and trust in building long-term relationships with our customers. That's why we welcome customers to audit our facilities at any time.
We believe that this demonstrates our commitment to providing our customers with the highest quality products and services. It allows customers to see firsthand how we operate, and how we ensure that our products meet the highest standards of quality and performance.
We invite our customers to visit our facilities at any time, and we will be happy to provide a tour and answer any questions you may have about our processes and procedures. We believe that this allows us to build trust and confidence with our customers and helps us to continuously improve our processes.
By welcoming your audit, we are also giving you the opportunity to witness the stringent quality measures we take to ensure our products meet the highest standards of quality, reliability and performance.
We look forward to welcoming you to our facilities and showing you firsthand the level of quality and commitment that goes into every product we produce.
Our Quality Policy
At Rasph Corp, we are committed to providing our customers with the highest level of quality and reliability in our wire harness and cable assembly products and services. We strive to be a leader in the industry by consistently meeting or exceeding customer expectations and industry standards.
Our Quality Policy guides us in our goal of being a high-reliability manufacturer of cables and harnesses. We are dedicated to meeting or exceeding customer-directed quality requirements, as well as all applicable statutory or regulatory requirements while providing on-time deliveries at a competitive price.
To achieve this goal, we have implemented a comprehensive quality management system that includes:
- A dedicated quality team that oversees every step of the production process, from Design and Engineering to Manufacturing and Testing.
- Advanced testing equipment and techniques to thoroughly test our products before they are delivered to our customers. This includes both in-process and final inspection to ensure that the product meets the required specifications.
- A commitment to continuous improvement, which allows us to identify and address any issues that may arise during the production process, and implement corrective actions.
- A commitment to providing our team members with the training and tools they need to produce high-quality products, including IPC/WHMA-A-620 Workmanship Standards for Cable and Harness Assembly.
- A commitment to achieving our ISO 9001:2015and AS 9100 certification and contracting out with a consulting group to help us in this effort.
- Customers can audit our facility at any time.
- Our ultimate goal is to achieve total customer satisfaction by providing quality products and services that meet or exceed their expectations. We believe that by continuously improving our processes and procedures, we can achieve this goal.
Job-Specific Training & Workmanship
At Rasph Corp, we believe that providing our employees with the proper training and tools is essential to producing high-quality products. That's why we have made it a priority to ensure that all of our employees receive job-specific training that is tailored to their specific roles within the company.
One of the key components of our training program is IPC/WHMA-A-620 Rev E and J-STD-001 Rev H. These industry-standard training programs cover all aspects of cable and harness assembly, including proper soldering techniques, wire preparation, and inspection procedures.
To ensure that our employees receive the best possible training, we bring certified IPC trainers to our facility to train our employees in these standards. This allows us to provide our employees with the knowledge and skills they need to produce high-quality products that meet or exceed industry standards.
We are also a member of IPC (Association Connecting Electronics Industries) and WHMA (Wire Harness Manufacturers Association) which helps us to stay updated on the latest industry standards and best practices.
We believe that by providing our employees with this training, we are able to ensure that all of our products meet the highest industry standards for quality and workmanship. This, in turn, enables us to provide our customers with products that are reliable, consistent and perform to the highest levels.
At Rasph Corp, we understand the importance of providing our customers with high-quality products and services. Quality is an integral part of our production process and we make sure to implement it at every step. From design and Engineering to manufacturing and testing, our team members are responsible for ensuring that our products and services meet or exceed customer expectations and industry standards.
Contact UsOur Assurance
Quality Assurance and Delivery Performance Monitoring
- Corrective action request (CAR)
- Non-Conforming Material Report (NCMR)
- Defect Tracking & Traceability
- On-time delivery metric
- Yield/efficiency tracking
- Root cause analysis
- Regularly scheduled evaluations of quality and on-time delivery performance at intervals of daily, weekly and quarterly
- Constant improvement in quality and delivery performance
- Regularly review and assess performance to meet customer requirements and expectations
Documentation
- Detailed documentation of all processes
- Easy to identify and resolve issues
- Maintaining records of performance, inspection, and testing results
- Regular review and update of documentation to ensure compliance with industry standards
EHS
At Rasph Corp, we place a strong emphasis on ensuring the well-being of our employees and protecting the environment. We are committed to professionally managing waste materials and implementing measures to safeguard the health of our workforce.
Environment
Rasph Corp recognizes the importance of environmental preservation. We are dedicated to minimizing our environmental footprint through responsible waste management practices. Our company strictly adheres to guidelines and regulations for the disposal of waste materials, including those generated during soldering processes. We aim to prevent any adverse impact on the environment and actively contribute to a sustainable future.
Health
The health of our employees is of utmost importance to us. We prioritize their well-being by implementing various measures to ensure their physical health is not compromised. Regular hand exercises are encouraged and conducted at set intervals to reduce physical strain. Additionally, we prioritize the use of Solder Smoke Absorbers and a Safety Mask to effectively capture and eliminate the flux smoke produced during soldering. These measures are in place to maintain a healthy work environment and minimize any potential health risks associated with soldering activities.
Safety
At Rasph Corp, safety is ingrained in our culture. We take extensive measures to create a safe working environment for all employees. We understand the importance of protecting the eyes, and therefore, safety glasses are mandated for all employees. These glasses act as a protective barrier, ensuring that no particles or debris enter the eyes during work processes. We also maintain a vigilant approach to identifying and addressing potential hazards, such as tripping hazards or liquid leaks, to eliminate any risks to our employees' safety.
At Rasph Corp, we hold ourselves accountable for maintaining the highest standards of safety, health, and environmental responsibility. We continually assess and improve our practices to exceed regulatory requirements. Our commitment to professionally disposing of waste materials, promoting employee health through regular exercises and the use of Solder Smoke Absorbers, and enforcing safety measures like mandatory safety glasses, equipment safety guards, PPE, demonstrates our dedication to providing a secure and sustainable workplace for all employees.